Looking to learn?
Explore our learning resources
Learning
Kick-start a career in building conservation, with our advice on skills and training. We also have learning resources and activities to inspire younger learners.




Training and learning events
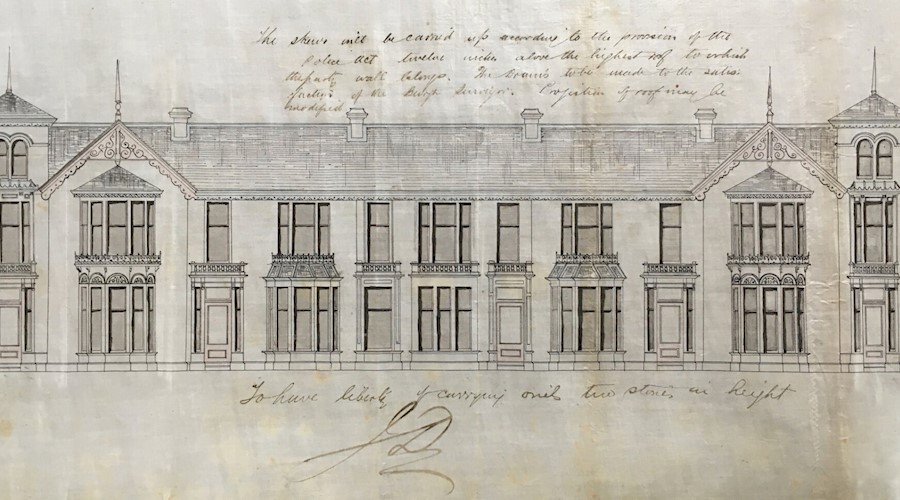
Researching Scotland’s Buildings
Wed 15 May 2024
An introduction to research sources and methods for architectural and construction history in Scotland. We will also share updates on the planned improvements to HES Archives facilities and collections.
Engine Shed
Enthusiast, Professional
Quite technical
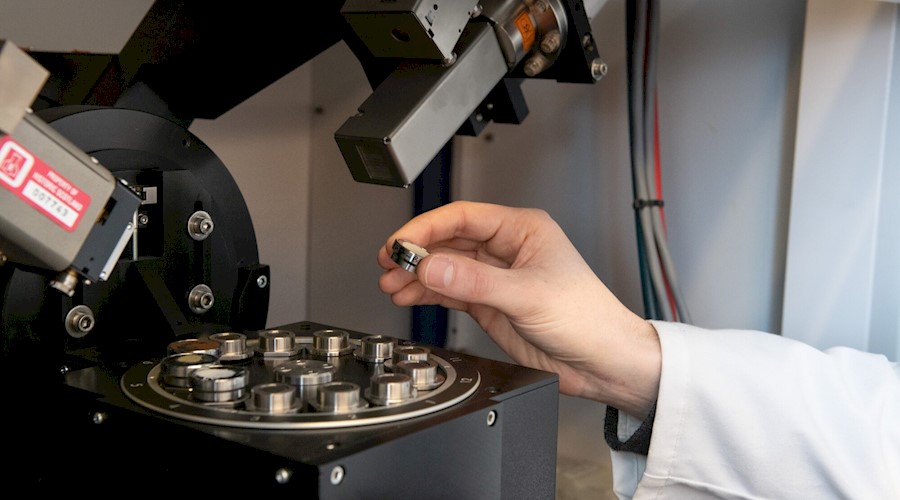
Heritage Science at the Engine Shed
Wed 22 May 2024
An introduction to the applied use of material science in heritage conservation in Scotland.
Engine Shed
Enthusiast, Professional
Quite technical
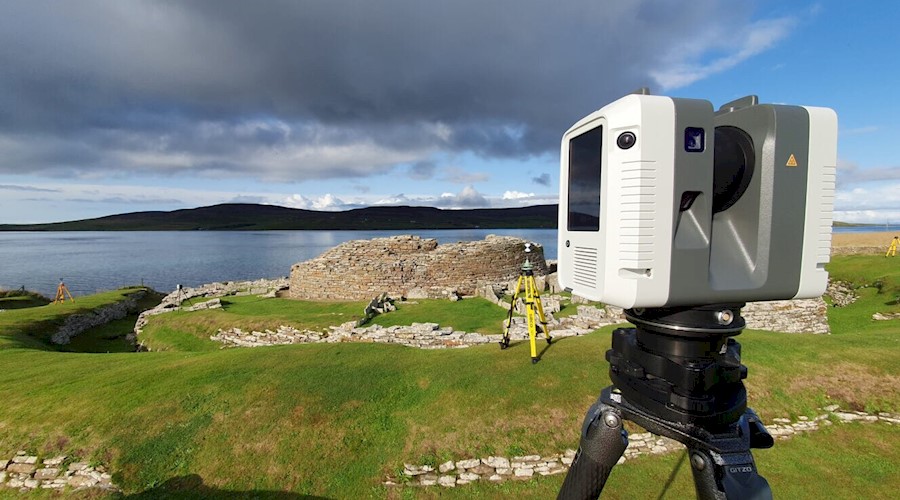
Documenting Scotland’s Historic Environment
Wed 29 May 2024
An introduction to a range of traditional and innovative methods for recording Scotland’s historic built environment.
Engine Shed
Enthusiast, Professional
Quite technical
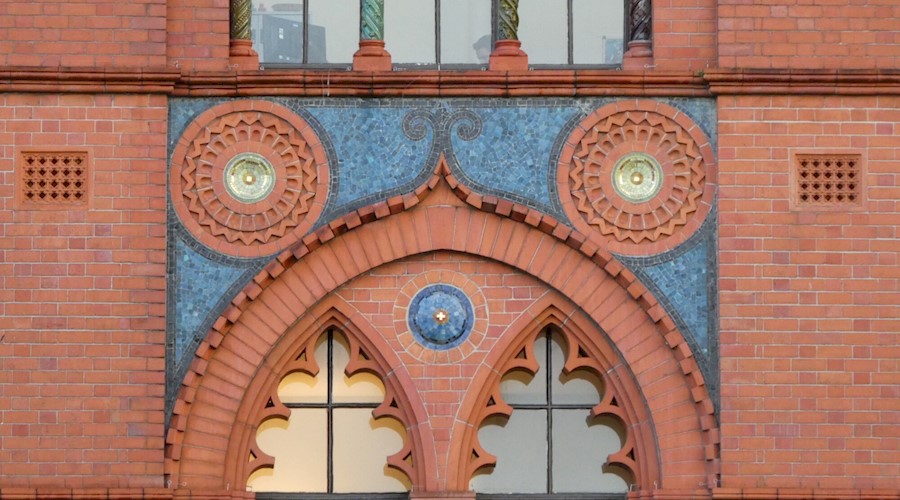
Historic Bricks and Tiles
Wed 5 Jun 2024
An introduction to the conservation of fired clay products in Scotland’s historic built environment, with a focus on historic brickwork and tiling.
Engine Shed
Enthusiast, Professional
Quite technical
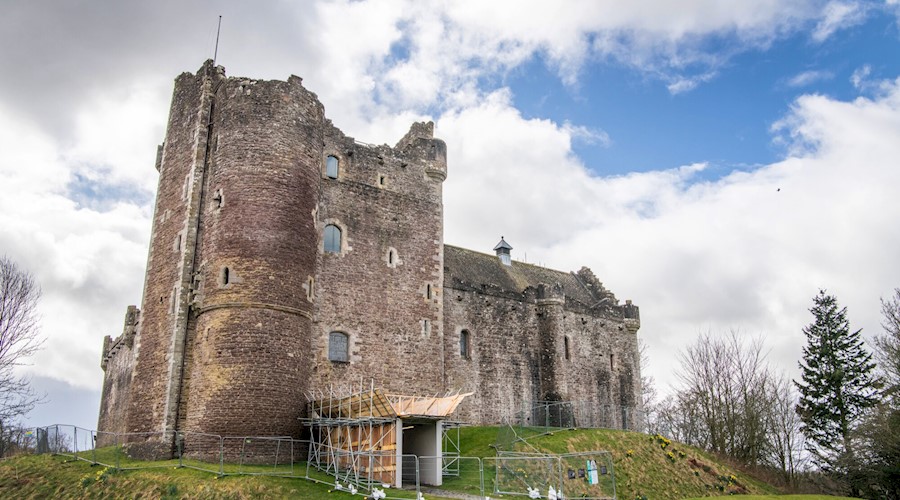
Introduction to Building Conservation Week
Mon 10 Jun 2024 to Fri 14 Jun 2024
Through a series of lectures and site visits, this 5-day course will explore conservation of the Scottish Built Environment and Traditional Building Skills.
Engine Shed
Enthusiast, Professional
Quite technical